Auto Replenishment in the Retail Scenario: A Competitive Advantage for Indian Retailers

The Indian retail market is a fiercely competitive landscape. Retailers are constantly striving to strike a balance between two crucial objectives: enhancing customer loyalty through exceptional service and minimising operational costs to maintain a competitive edge. This is where Automatic Store Replenishment (ASR) emerges as a game-changer.
What is Automatic Store Replenishment?
ASR is a technology-driven inventory management process that automates stock replenishment in retail stores. It utilises data from inventory management systems and point-of-sale (POS) systems to determine precisely when and how much stock needs to be reordered for each location.
Retailers can establish rules and configure algorithms within the ASR system. These algorithms consider various factors like sales velocity (how quickly a product sells), current stock levels, lead times (time taken to receive new stock from suppliers), and historical sales data. By analysing this data, the system calculates optimal reorder quantities, ensuring stores maintain adequate stock levels to meet customer demand without the risk of overstocking or stockouts.
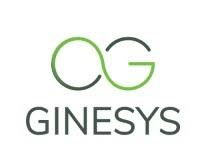
Say Goodbye to Stockouts: Harness the Benefits of Automated Store Replenishment!
The ASR Process Explained:
- Monitoring and Data Collection: POS systems and inventory management systems continuously collect data on sales, stock levels, and customer demand. This data can be real-time or collected at regular intervals.
- Demand Forecasting: Advanced algorithms analyse the collected data and predict future demand patterns for each store and product.
- Reorder Point Calculation: Based on factors like desired service levels, lead times, and safety stock levels (minimum inventory to avoid stockouts), the system determines reorder points. These points signify when stock needs to be replenished.
- Automatic Reordering: When the stock level of a particular item falls below the reorder point, an automatic reorder is triggered. This process can be facilitated by integrating the inventory management system with suppliers for seamless and efficient replenishment.
- Order Processing and Delivery: The automatic reorder requests are processed and sent to suppliers, who fulfil the orders and deliver the required stock to the stores.
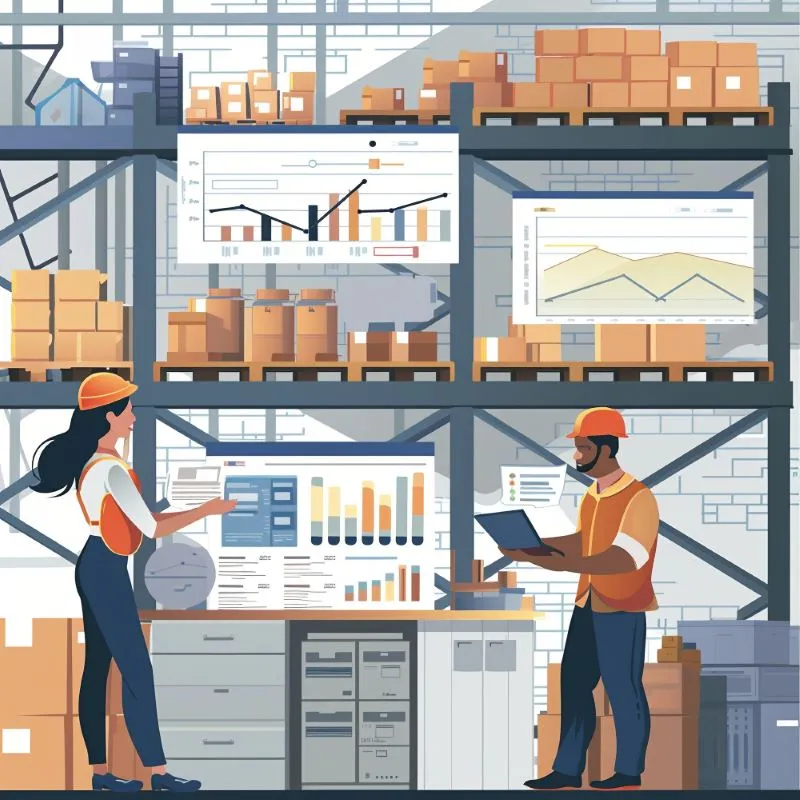
Benefits of Automatic Store Replenishment for Indian Retailers:
Automatic Store Replenishment offers a multitude of advantages that can significantly enhance a retailer's operations in the Indian market. Here's a closer look at some key benefits:
- Reduced Out-of-Stock Situations and Increased Sales: Empty shelves translate to lost sales and customer frustration. Customers who encounter out-of-stock items often purchase them elsewhere, potentially leading to brand substitution and lost sales for manufacturers of strong brands as well. Studies indicate that in-store manual ordering mistakes are a major contributor to out-of-stocks, accounting for nearly 50% of them. ASR helps eliminate these errors by providing accurate forecasts and optimising stock levels, ultimately leading to higher sales and satisfied customers.
- Lower Inventory Costs and Improved Margins: ASR empowers retailers to choose between different ordering techniques, such as "Fill-to-Minimum" or "Fill-to-Maximum." Fill-to-Minimum keeps stock levels just above the minimum threshold, while Fill-to-Maximum ensures shelves are always full. ASR aids in determining the most suitable approach based on individual needs, potentially leading to significant cost savings.
- Reduced Labour Costs Through Cycle-Counting: Implementing ASR in retail stores replaces manual ordering with automated processes, resulting in reduced labour costs. Cycle-counting, a technique for maintaining accurate stock data, becomes a more efficient process. Instead of conducting full stock checks at every ordering cycle, retailers can perform cycle-counts every 4-8 weeks, further minimising labour costs.
- Minimised Price Markdowns: Fashion retailers typically budget for item procurement and distribution at the beginning of each season. This often results in leftover stock at the end of the season that must be heavily discounted due to low customer demand. ASR, with its focus on item-level turnover planning and inventory control, enables retailers to monitor sales trends throughout the season. This allows for timely price adjustments, potentially reducing overall markdowns at the end of the season.
- Reduced Reliance on Loss Leaders for Impulse Buying: Logistics and commercial needs often clash in retail. Logistics managers prefer infrequent deliveries to minimise distribution costs, while commercial teams prioritise low store inventories, high delivery frequencies, and minimal stockouts. Auto Replenishment in retail helps bridge this gap by enabling high delivery frequencies without compromising overall efficiency. Additionally, item-level inventory control ensures low on-shelf visibility while maintaining sufficient backroom stock, reducing the reliance on discounted "loss leaders" to stimulate impulse purchases.
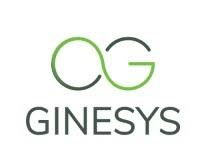
Transform Your Inventory: Embrace Automated Store Replenishment
Factors Critical for ASR Success:
- Data Integrity at Implementation: Accurate and reliable data at the start of the ASR implementation process is crucial for optimal system performance.
- Effective Forecasting and Order Algorithms: Developing accurate forecasting models and order algorithms that minimise manual interventions is essential for successful ASR implementation in retail.
- Utilising ASR Information for Maximum Benefit: Retailers need to leverage the insights and data generated by the ASR system to their full potential. This includes continuously monitoring system performance, identifying areas for improvement, and adapting strategies based on real-time data.
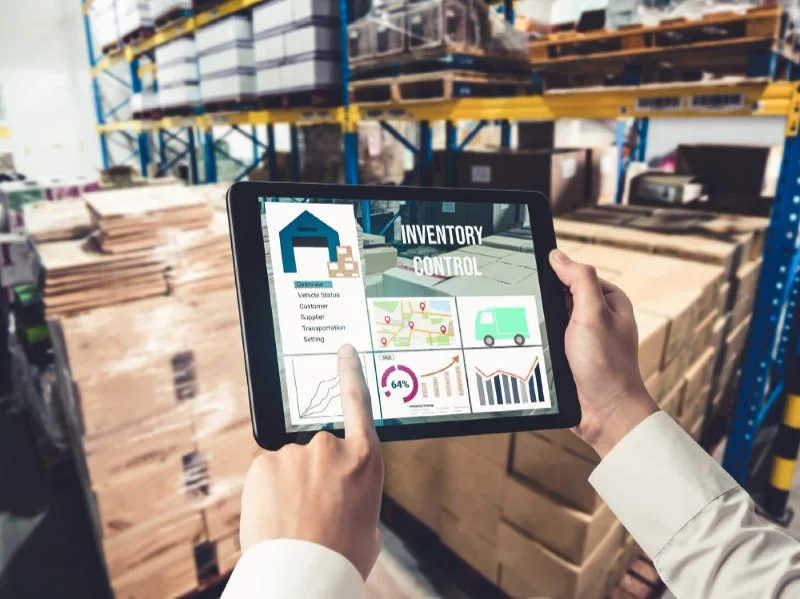
Ginesys One and Supplymint: A Powerful Combination for Retail ASR
Ginesys One, a comprehensive omnichannel retail suite, offers seamless integration with Supplymint's DigiARS, a cloud-based auto replenishment system. DigiARS empowers retailers to make informed decisions regarding adding or removing inventory for specific items or categories. This integration is fully automated, eliminating the need for manual intervention.
For retailers seeking a streamlined and efficient store replenishment solution, the Ginesys One and Supplymint combination is a perfect fit. The ease of setup, customization, and operation make it an ideal choice for businesses looking to optimise their inventory management strategies.
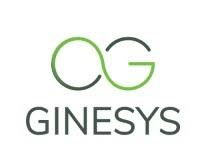
Empower Your Retail Business: Implement Automated Store Replenishment Now!
Embrace ASR and Gain a Competitive Edge
In today's fiercely competitive Indian retail sector, implementing Automatic Store Replenishment offers a significant advantage. By automating inventory management, minimising stockouts, and optimising stock levels, ASR empowers retailers to enhance customer satisfaction, minimise costs, and ultimately achieve greater profitability.
Partnering with experienced implementers like Ginesys ensures a smooth transition and maximises the benefits of ASR for your retail business. With the right technology and expertise in place, you can transform your inventory management, gain a competitive edge, and unlock the full potential of your retail operations in the dynamic Indian market.